Nafion™ Tubing
Nafion™ tubing, a highly selective tubing that helps increase accuracy during gas analysis, while reducing risk of damage to your device from condensation. The Nafion™ polymer is unique in its ability to seamlessly transfer moisture from one side of a membrane to the other side as a first order kinetic reaction.
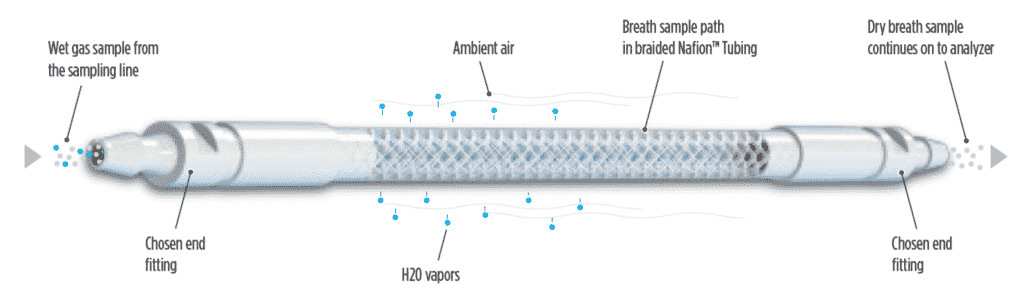
Nafion™ Technology
The Nafion™ polymer transfers water molecules from one side of the membrane to the other by a first order kinetic reaction. This is unlike a porous membrane that depends on the physical size of molecules. Nafion™ Polymer selectivity is based on chemical reactivity, not the size of the molecule – therefore, not traditional permeation. The Nafion™ polymer selectively transfers water vapors, leaving most analytes in the gas stream untouched.
The driving force for the Nafion™ polymer to transfer water molecules is the difference in humidity levels on either side of its membrane. The Nafion™ polymer aims to attain equilibrium of the partial pressure of water vapor on the inside and the outside of its membrane.
Chemical Properties of Nafion™ Polymer
The Nafion™ polymer was invented by Walther Groth in late 1960s. Nafion™ polymer is a copolymer of perfluoro-3,6-dioxa-4-methyl-7octene-sulfonic acid and tetrafluoroethylene (Teflon™). In simpler terms, Nafion™ polymer is a Teflon™ backbone with occasional side chains of another fluorocarbon. The side chain terminates in a sulfonic acid (-SO3H).
Apart from the sulfonic acid group, the Nafion™ polymer is a fluorocarbon. Like most fluoropolymers, it is extremely resistant to chemical attack (corrosion resistant). The sulfonic acid group is immobilized within the bulk fluorocarbon matrix and cannot be removed, but unlike the fluorocarbon matrix the sulfonic acid groups do participate in chemical reactions. The presence of the sulfonic acid adds three important properties to Nafion polymer:
- Nafion™ polymer functions as an acid catalyst due to the strongly acid properties of the sulfonic acid group.
- Nafion™ polymer functions as an ion exchange resin when exposed to solutions.
- Nafion™ polymer very readily absorbs water, from the vapor phase or from the liquid phase. Each sulfonic acid group will absorb up to 13 molecules of water. The sulfonic acid groups form ionic channels through the bulk hydrophobic polymer, and water is very readily transported through these channels. Nafion™ polymer functions like a very selective, semi-permeable membrane to water vapor.
The physical properties of Nafion™ polymer are similar to those of other fluoropolymers. It is a translucent plastic. When used as an ion exchange membrane, it operates at temperatures up to 190°C. When used as a dryer, it can operate at temperatures of up to 150°C. The burst pressure of Nafion™ tubing is generally greater than 200 psig (over 13 bar) but it varies with the diameter and wall thickness. An unusual property of Nafion™ polymer is its propensity to change in physical size. As Nafion™ polymer absorbs water, it swells by up to 22%. When exposed to alcohols it increases in size by up to 88%.
It’s highly selective nature makes the Nafion™ polymer ideal for analysis applications where moisture needs to be removed without analyte loss.
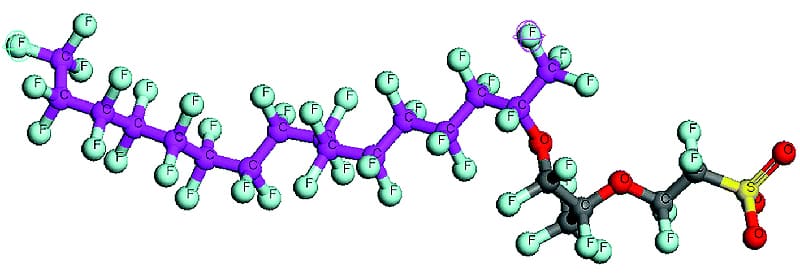
Nafion™ Polymer Permeability
Removed by Nafion™ Polymer | |
---|---|
Atmospheric Gases | H20 |
Inorganics | NH3 |
Organics | Alcohols, DMSO, THF |
Variable Losses | |
Organics | Acids, Aldehydes, Amines, Ketones, Nitriles |
Nafion™ Polymer Impermeability
Retained in Sample | |
---|---|
Atmospheric Gases | Ar, He, H2, N2, O2, O3 |
Halogens | Br2, Cl2, F2, l2 |
Hydrocarbons | Simple Forms (Alkanes) |
Inorganic Acids | AHCL, HF, HNO3, H2SO4 |
Other Organics | Aromatics, Esters, Ethers |
Oxides | CO, CO2, SOX, NOX |
Sulfur | COS, H2S, Mercaptans |
Toxic Gases | COCL2, HCN, NOCl |
Gas Permeability of Nafion™ Polymer and Water
We are often asked about the relative selectivity of water in Nafion™ polymer relative to common gasses. Please see the graph for the relative gas permeability of water through Nafion versus some common gases. As you can see, Nafion is very effective at transporting only water while keeping the other gasses separated. For example, for every 1,000,000 water molecules that pass through Nafion™ polymer, 1000 H2S or CO2 molecules would pass through Nafion™ polymer. In the same sense, for every 1,000,000 water molecules that pass through Nafion™ polymer, 1 O2 or N2 molecule would pass through Nafion™ polymer.
Certifications for our ME Dryers
Our Nafion™ tubing dryers have 510(k) approval and can be produced in our FDA-registered, CGMP compliant clean room to your specifications. From tubing to entire sample lines with your labeling and UDIs, we can support your drying applications.
We’ve evolved our manufacturing and testing capabilities to ensure that superior quality.
- ISO 9001 and ISO 13485 Certified
- Products 100% Tested for Leak and Flow
- FDA Registered With 510K For Nafion™ Tubing Dryer
- ISO Class 8 Clean Room
- Proprietary Nafion™ Tubing Conversion to Activate Moisture Transfer Properties
- In-House Extrusion and Injection Molding
- Manufacturing Engineering to procure and validate new technologies to produce custom products
- Unique Device Identifier Compliant Packaging
Regulatory bodies constantly update standards to ensure the highest level of care is delivered to patients. Our Engineering team is well versed in these standards, including the latest ISO 80601-2-74 released in 2017.